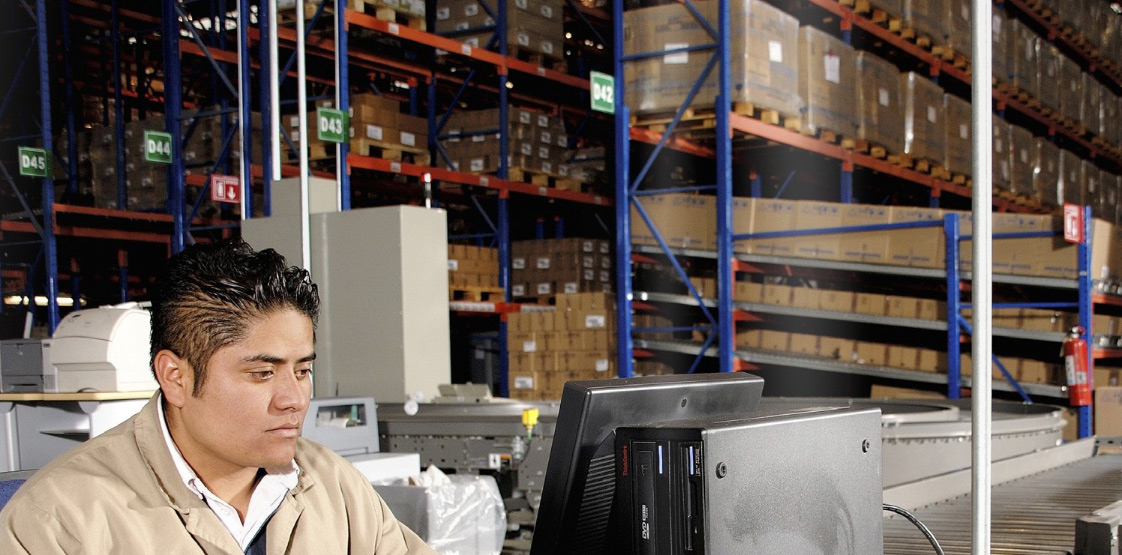
Thomas R. Cutler discusses with Joel Boss of Integrated Systems Group how to avoid failures when updating a distribution center.
The most common areas of quality failure in a distribution center and manufacturing material handling process are communication, documentation and budget. Integrated Systems Group (ISG) utilizes a documented process, says engineering manager, Joel Bos. “It is imperative that the software requirement, as well as the deliverable, be documented thoroughly. This insures that the customer’s wants versus needs are identified and expectations met. The result is a clear picture for both parties to understand. It takes due diligence during the design cycle to ensure that all of the needs are documented upfront and a future growth plan is in place. If shortcuts are made quality problems will ensue.”
This is not ISO 9001, nor is it a six sigma project. The best documentation to ensure quality when updating a distribution center starts out with a thorough analysis of the client’s item master and existing operational processes; this is followed up with an equipment, software and process analysis. “Close attention is given to the operators and interviews are conducted to identify problems or short-comings in the existing processes,” says Bos. “It is critical to work with the client to determine future growth and other business rules.”
The entire warehouse process must be flow-charted and thoroughly documented. In most cases there is planned growth for the business. Other factors can also include planned SKU growth, mergers and consolidations. “When these items are analyzed and plugged into the ISG software certain outcomes are derived,” Bos explains. “We can take a look at how processes can be improved and what the size of the projected building should be to conduct the level of business desired. ISG also compares the present day operation to industry standards and draws conclusions for correction as well.”
A gap analysis
A gap analysis of the software can be conducted once the information above is gathered. The gap analysis is a critical tool that helps a distribution center to compare its actual performance with its potential performance. At its core are two questions: “where are we?” and “where do we want to be?”
The specific benefit of a gap analysis in the distribution center environment is a visual comparison of present day software capabilities versus what is needed to drive the warehouse and operations designed and discussed above. This analysis is designed to look at streamlining the operations with a consolidated software package or automated pick system.
Bos has seen some remarkable impacts from the gap analysis. “In some cases we can suggest designs that reduce picking and packing staff by 60 percent and at the same time increase throughput 30-40 percent, simply by designing the right equipment into the warehouse and optimizing the layout and properly slotting the SKUs.”
After extensive scenario planning, due diligence, and listening, a complete design is reviewed with a budget price and projected return on investment. The companies must then determine if pricing is within their affordability range. If not, then the paring down process begins and this is where “wants vs. needs” comes into play. In some cases a phased plan is suggested to incorporate the entire scope of work just over a multi-year span. Each distribution center has different business rules, growth plans, and levels of automation to consider.
Quick and temporary fixes cost more
Too often there is a perception by some executives in the industrial sector that the warehouse gets the last look for budget and equipment improvements. This narrow vision can lead to quality failures such as temporary fixes that do not fully address an issue and result in poor implementation.
Bos explained why ISG believes the warehouse should not be overlooked. “Not all firms look at things from a lean perspective. When the time comes for the department heads to submit their budgets, the typical things that get priority are sales and marketing and product development. The warehouse tends to be way down on the list. Too often the warehouse is viewed as simply a means of filling and shipping orders, or an evil necessity to conduct business. However, the department head that recognizes the cost of mis-picked items, the costs of short picks, or the cost of returned goods…or that there are better ways to accomplish things in the warehouse, is going to get upper management’s attention and appreciation.”
Quick fixes such as multiple software packages that may appear to solve some distribution center and warehouse problems usually require the users to toggle between many screens. In the future when the budget money is available, some or most of these packages will be obsolete and end up wasting company money.
Third party shipping software that does not easily interface to the host software frequently results in data entry errors, poor quality, and increased time wasted by users on multiple systems. “Another example of a quick fix is adding a warehouse module (WM) that your host software provider recommends,” said Bos. “It is touted to be everything you need and is compatible with the host. The pitfall is that most host packages focus on inventory and accounting. They do not typically excel on warehouse functions and so the promise looks good but the deliverable is less than expected. Some of this software may be thrown away a year or two later when the inabilities are surfaced and the need for a warehouse control system (WCS) solution is realized. Most WCS packages include an integrated shipping screen/solution, packing screens, quality screens, and are designed to deal with a myriad of warehouse functions and equipment.”
Another quick fix is to simply add more rack to a facility. This may gain more storage locations quickly but may increase actual pick times. A short time later the warehouse manager may find those same rack locations need to be torn down to make room for a multi-level pick module, which provides a means for more efficient picks.
Distribution centers: a quality contingency plan
From the warehouse project inception there must be a quality contingency plan. Each critical point must be reviewed and a documented plan for unforeseen failures must be established.
While few failures occur, operators and management must be trained to properly respond in the event a quality problem ensues. Documentation for the quality process usually includes details from software procedures, picking and packing procedures, to wave release and staffing issues. It also covers conveyor, sortation and workstation issues.
“Backup or contingency plans are essential and can be as simple as installing a few host terminals around the facility,” said Bos. “But it is always part of the design to make sure product gets shipped.”
The costs of poor quality in the warehouse distribution center
There are real costs for poor quality in the warehouse distribution center, including:
- Short picks cause multiple shipments. This in turn causes increased shipping charges and disappointed customers.
- Poor inventory control or inaccurate picking can result in late fees and/or penalties from customers. They can also lead to an increase in returned goods and related processing.
- Poor management of the software deliverable could cause additional site time and implementation time. If the software vendor is late in delivering the goods and exceeds the implementation window, it may result in a significant cost with idle workers and irate customers who were expecting delivery when promised.
- Warehouse managers and distribution center operations and quality professionals could find their jobs in jeopardy if company executives feel proper due diligence was not conducted.
Selecting the best material handling providers
A lot of suppliers in the material handling world say that they can “do everything.” Select a provider that has a history of repeat customers where technical solutions were successfully implemented. Also be aware of providers that are promoting a solution with a large amount of their own product. In those cases there is an obvious bias. Avoid providers that design in a vacuum and don’t listen to the specific needs of that warehouse operation. Select a single provider or integrator that can provide all of the facets of the system you need to avoid finger pointing, resulting in a shorter implementation and a successful system.
Ensure that distribution center consultants have provided clients with improved quality solutions for replenishing, picking, packing and manifesting. Those methods must be proven to make pickers and packers more efficient; reporting screens give important data to managers and supervisors to show which employees are efficient and which ones are making repeated mistakes.
* * *
Thomas R. Cutler is president & CEO of Fort Lauderdale, Florida-based, TR Cutler, Inc., and founder of the Manufacturing Media Consortium of journalists and editors writing about trends in manufacturing. www.trcutlerinc.com